Экологически чистые дисперсионные краски Сaparol
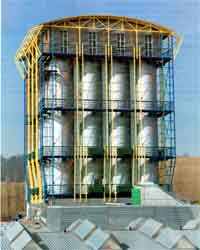
История развития
Предприятие Deutsche Amphibolin-Werke von Robert Murjahn было основано в 1895 году в городе Обере-Рамштадте . Тогда предприятие специализировалось на добыче из горных пород асбестосодержащего минерала амфиболина. Позднее фирма стала заниматься изготовлением материалов для покрытий, используемых в строительной сфере (например, известково-казеиновых связующих). В 30-е годы на заводе была освоена технология производства синтетических дисперсионных связующих. Это событие открыло новый этап в истории развития предприятия: с того времени научные исследования и разработки, ведущие к появлению более совершенных материалов, стали неотъемлемой частью деятельности фирмы. Большая роль на предприятии стала отводится высококвалифицированным специалистам, работающим в русле последних достижений научно-технического прогресса. Такая стратегия сохранилась на фирме и до наших дней. Неудивительно, ведь она сразу же принесла и продолжает приносить прекрасные результаты. Универсальные связующие для красок Сaparol (казеин, парафин, различные виды масел) и разработанные несколько позднее дисперсионные материалы на базе природного сырья совершили самую настоящую революцию на рынке отделочных материалов Германии и всей Европы. В течение многих лет изделия марки Alpinaweis являются самой покупаемой разновидностью дисперсионных красок в Европе. Благодаря исследованиям и разработкам, постоянно проводимым фирмой, ее продукция продолжает удерживать свои высокие позиции на потребительском рынке. Так, например, в 1985 году предприятием была разработана краска для внутренних отделочных работ Indeko-plus, не содержащая вредных для здоровья людей связующих и не выделяющая вредных эмиссий. Уже более десяти лет этот материал занимает "пальму первенства" среди выпускаемой во всей Европе продукции для малярных работ.
Последующие разработки в данной области - фасадные краски Amphibolin, Muresko и AmphiSilan, краски для внутренних отделочных работ Alpinaweis, Malerit и Indeko-plus, многочисленные специальные продукты - благодаря своему высокому качеству также заняли свое достойное место на европейском рынке материалов для строительства и ремонта.
Сегодня предприятие Deutsche Amphibolin-Werke von Robert Murjahnработает по трем основным направлениям: Caparol производит краски и системы покрытий, Capatect занимается теплоизоляционными и композиционными системами, Disbon специализируется на создании материалов для защиты и ремонта строительных сооружений. Продолжая проводить свою политику, фирма стала пионером в области распространения дисперсионных технологий во многих европейских странах. Сегодня современные заводы и фабрики в Австрии, Франции и Италии, основанные фирмой, выпускают высококачественные дисперсионные материалы. В последние годы предприятие начало сотрудничать и со странами, находящимися на постсоветском пространстве, передавая им свой опыт и профессиональные знания.
Этот опыт интересен не только с точки зрения рыночно-потребительских свойств материалов и технологий, используемых фирмой. Само производство высококачественных изделий также заслуживает внимания.
Фабрика в Обер-Рамштадте
В 1993 году предприятие Deutsche Amphibolin-Werke von Robert Murjahnи по производству красок в городе Обер-Рамшатдт, работающей с 1895 года. 28 июня 1995 года было начато строительство башенного комплекса резервуаров. 18 июля началось возведение металлического каркаса башни. В сентябре следующего года 16 резервуаров, входящих в состав башни, были готовы. Тяжелые промышленные емкости, весящие более 29 тонн, поднимались на требуемую высоту и устанавливались на отведенное место при помощи двух башенных кранов. Для доставки емкостей на место строительства использовались специальные транспортные средства.
Такова история реконструкции фабрики, рассказанная в двух словах. На практике каждый этап реализации был связан с различными техническими, экономическими и социальными нюансами, заслуживающими отдельного внимания.
Когда объект находился на стадии проектирования, граждане маленького округа Обер-Рамштадт высказались против строительства. Их претензии были рассмотрены и учтены в срочном порядке. В результате проект претерпел существенные изменения: в своем новом варианте резервуарная башня фабрики должна была быть на десять метров ниже, чем это предполагалось ранее. Из-за корректировок, вносимых в проект, запуск производства произошел позже запланированных сроков. Но нет худа без добра - в результате всей этой истории интерес общественности к реконструкции фабрики значительно возрос.
Итак, согласно новому проектному решению, было возведено сооружение из 16 резервуаров высотой 24 м. Для его строительства были использованы специальные свайные фундаменты, глубоко погруженные в грунт. "При возведении башни была применена конструкция абсолютно нового типа. Для того, чтобы возвести по апробированной строительной технологии металлический каркас, обладающий повышенной огнестойкостью и сейсмостойкостью, потребовалось использовать в фундаменте сооружения 50 бетонных свай диаметром 90 см и глубиной 20 м, способных передавать нагрузку на глубоко залегающие в грунте скалистые горные породы", - заявил менеджер проекта профессор доктор Вольфганг Резель. Весь несущий металлический каркаса башни высотой 39 м был смонтирован всего лишь за восемь недель.
"Благодаря новой автоматизированной технологии, примененной на фабрике, удалось снизить количество отходов производства. Так как сырье поступает на производство непосредственно со специализированных транспортных средств, ежегодно экономится до 250 тонн упаковочных материалов", - прокомментировал ситуацию консультант по вопросам экологии Петер Буркарт, подчеркивая при этом экономические преимущества использованного решения. В новом промышленном сооружении для получения красок используются твердые сырьевые материалы. Из 20 отсеков резервуаров (объемом 180 м2 каждый) при помощи специальных винтовых подъемников сырье поступает на весы, а затем - в смесительные установки.
Использование прогрессивной технологии производства позволило добиться следующих преимуществ. Во-первых, поскольку при производстве не применяются дизельные установки, достигается значительное снижение шума. Во-вторых, производство характеризуется высокой степенью чистоты и стерильности. И наконец, большим преимуществом является большая производительность нового промышленного сооружения - начиная со следующего года, планируется увеличение объемов выпускаемой продукции на 100 000 тонн ежегодно.
Модернизация по самым современным стандартам
Сегодня новая фабрика в Обер-Рамштадте ежедневно производит 1000 тонн красок. Но не только это производство, на котором сейчас занято 1350 человек, было реконструировано предприятием Deutsche Amphibolin-Werke von Robert Murjahn. Еще несколько промышленных объектов, находящихся в Берлине, Фюрстенвальде, Кетхене и Нерхау, были модернизированы на средства, вложенные фирмой. Начиная с мая 1992 года, перечисленные фабрики в Восточногерманских землях перешли в ведение группы фирм Caparol. Благодаря проведенным преобразованиям данные предприятия стали производителями широкого спектра красок.
Модернизацию завода в Обер-Рамштадте можно расценивать не только как прорыв на рынке отделочных материалов. Это событие также открыло целый ряд технических новшеств в производственном цикле, которые отразились на архитектуре самого объекта. Новые дисперсионные резервуары, трубопроводы, объединенные в так называемый "средовой канал", а также увеличение высоты промышленного здания на участке старого производства стали предпосылками для возведения башни резервуаров.
"Средовой канал" соединил резервуары для хранения дисперсионных материалов с основным производственным объемом. 32 трубопровода, проходящие через канал, транспортировали дисперсионные связующие к "хайтековской" башне резервуаров. Между складом готовой продукции и основным производством был выполнен так называемый энергетический мост. В эту конструкцию были спрятаны все важнейшие сети и устройства электропроводки, включая трансформаторы и выключатели. Так было решено централизованное обеспечение производства электроэнергией.
Увеличение высоты промышленного корпуса на 4,5 м было продиктовано требованиями по расширению площадей, необходимых для производства. В полученном таким образом пространстве были установлены новые инженерные сети для подводки дисперсионных масс и инсталлирована дополнительная техника. Работы по реконструкции цеха были начаты летом 1994 года, а закончены в марте 1995 года. Крыша объекта была также оборудована пылеулавливающими фильтрами, которые обеспечили защиту рабочих мест в цеху от воздействия вредных частиц пыли.
Дисперсионные резервуары были запущены в производство 28 февраля 1995 года. Из-за зыбких грунтов на участке, отведенном для этих сооружений, ведение строительных работ оказалось более сложным, чем это предполагалось ранее. В данном случае также были использованы свайные фундаменты (включающие в себя 21 сваю глубиной 27 м каждая). Металлический каркас для помещения дисперсионных резервуаров был собран за рекордно короткий срок - четыре недели. Одновременно со сборкой каркаса монтировались и сами резервуары для дисперсионных масс - 40 резервуаров объемом 30 м3, 2 резервуара объемом 18 м3 и 6 резервуаров объемом 12 м3.
В декабре 1994 года была инсталлирована сложнейшая система трубопроводов, общей протяженностью 8 км. Одновременно с этим производилась прокладка электрического кабеля общей протяженностью 35 км. В качестве архитектурного связующего элемента между цехом дисперсионных резервуаров и основной башней были использованы три "финишные" станции, предназначенные для закачивания готовой продукции в баки специальных транспортных средств.
Реконструкция завода в Обер-Рамштадте стала событием новаторского плана благодаря не только современнейшему построению технологического процесса на производстве, но и необычной выдающейся архитектуре сооружения.
Светлана ЛОБАНОВА
Строительство и недвижимость. Статья была опубликована в номере 36 за 1997 год в рубрике лкм